3D printing, also known as additive manufacturing, is a process that creates three-dimensional objects by adding layers of material one by one based on a digital design. It’s like building something brick by brick, but the “bricks” are tiny layers of materials like plastics, metals, or resins. This technology has transformed how we make things, from rapid prototyping to producing final products, and is used in fields like healthcare, aerospace, and education.
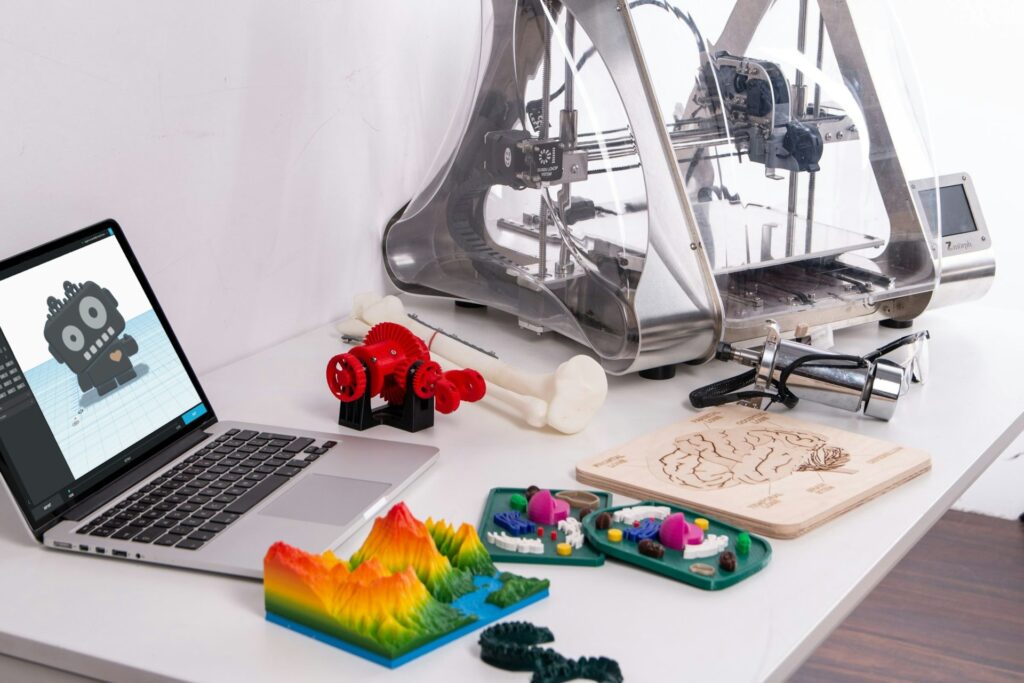
How Does It Work?
The process starts with a digital model, usually created using computer-aided design (CAD) software. This model is then sliced into thin layers, and the 3D printer uses this information to build the object layer by layer. The method of layer deposition varies depending on the technology, such as melting plastic for FDM or curing resin with a UV laser for SLA.
Why It Matters
3D printing offers flexibility and customization, allowing for complex shapes that traditional methods can’t easily achieve. It’s especially useful for creating custom medical devices, lightweight aircraft parts, and educational models, making it a game-changer in many industries.
Concise Analysis of 3D Printing Familiarity and Trends
Definition and Process
3D printing, or additive manufacturing, is the process of creating three-dimensional objects from a digital model by depositing, joining, or solidifying materials layer by layer. This method contrasts with subtractive manufacturing, where material is removed, and is known for its ability to produce complex geometries that traditional methods might struggle with. The process typically starts with a CAD (computer-aided design) file, which is sliced into layers and fed to the printer, which then builds the object from the bottom up. Common materials include plastics, metals, ceramics, and even bio-compatible resins, with ongoing research into advanced composites and biodegradable options.
Technologies in Depth
Several 3D printing technologies cater to diverse needs, each with unique strengths:
- Fused Deposition Modeling (FDM)/Fused Filament Fabrication (FFF): This is the most common technology, especially for consumer and educational use, involving melting a thermoplastic filament and depositing it layer by layer. It is cost-effective and widely accessible, with a 2021 survey indicating 71% of respondents used it in-house (Statista). It is ideal for rapid prototyping and simple functional parts, though it may lack the precision of other methods for fine details.
- Stereolithography (SLA): Utilizing a UV laser to cure liquid resin, SLA offers high precision and smooth surface finishes, making it suitable for detailed models and jewelry. It is noted for its accuracy but can be slower and more expensive, often used in dental and medical applications (Formlabs).
- Selective Laser Sintering (SLS): This method uses a laser to sinter powdered material, typically nylon, into solid structures, eliminating the need for support structures due to the unfused powder acting as support. It is excellent for complex geometries and functional prototypes, with strength comparable to injection-molded parts, and is popular in engineering for its mechanical properties (Formlabs).
Other technologies include Direct Metal Laser Sintering (DMLS) for metal parts, PolyJet for multi-material printing, and emerging methods like Multi-Jet Fusion (MJF) by HP, noted for faster printing and improved part quality (Sigma Design). The choice of technology depends on the application, material, and required precision, with FDM leading in accessibility and SLA/SLS in industrial precision.
Applications Across Industries
3D printing’s versatility has led to its adoption across numerous sectors, with significant impacts noted:
- Healthcare: It is revolutionizing medical fields by enabling custom prosthetics, dental aligners, and even bioprinting for tissue engineering. For instance, clear aligners are thermoformed on 3D-printed molds, a major success in dentistry (Formlabs). Bioprinting is advancing, with potential for organ fabrication, addressing organ donor shortages, and personalized medicine, particularly noted in 2025 trends (Cults3D). Recent advancements include miniature pancreas models and skin tissue bioprinting directly onto wounds.
- Aerospace and Automotive: These industries benefit from lightweight components that reduce fuel consumption and environmental impact. 3D printing allows for on-demand production of parts like metal brackets and turbine blades, with part consolidation simplifying assembly. It is also used for rapid prototyping and custom parts, with aerospace seeing increased use for safety-critical components (Forbes, AMFG).
- Education and Research: 3D printers are common in classrooms and libraries, facilitating STEM education through low-cost prototyping. Students can design and print models, bridging the gap from digital to physical, with companies like MakerBot offering certification courses (MakerBot). This hands-on approach prepares students for future innovation, with applications in scientific equipment fabrication from open hardware designs.
- Construction and Art: Large-format 3D printing is a 2025 trend, with projects like 400-square-foot houses printed in under 24 hours, useful for emergency shelters (Tech 21 Century). In art, it enables custom designs and sculptures, expanding creative possibilities. Specific projects in 2025 include the UCC project in Qatar with a 40,000 m² footprint, using real concrete for 5-10x lower costs and greater sustainability.
The market is projected to reach $101.74 billion by 2032, growing at a 23.4% CAGR from 2025, reflecting its expanding applications (Fortune Business Insights).
Recent Trends and Developments in 2025
In 2025, several trends are shaping the 3D printing landscape, reflecting its evolution and broader adoption:
- Material Innovation: New materials like conductive polymers, biodegradable plastics, and bio-based resins are gaining traction, driven by sustainability goals. Advanced metal alloys, such as NASA alloy GRX-810 and MIT titanium, are developed for aerospace and medical needs, enhancing performance (3DSPRO, Massivit).
- Large-Format Printing: This is advancing rapidly, particularly for aerospace, automotive, and construction, enabling customized, lightweight components at scale. It addresses challenges like material selection and printing speed, with ongoing research promising efficiency gains (Massivit).
- Speed and Efficiency: Innovations like Creality’s Hi Combo at CES 2025 and Bambu Lab’s flagship release in Q1 2025 highlight faster printing with multi-material capabilities, enhancing productivity (3DSPRO). AI integration is optimizing processes, particularly in bioprinting, improving precision (Cults3D).
- Sustainability and Accessibility: The focus on eco-friendly materials aligns with global sustainability goals, while desktop printers like those from Bambu Lab and Creality are becoming more affordable, democratizing access (Fabbaloo, CNET).
Notable projects include the development of high-performance nanostructured alloys for medical and aerospace applications, and large-scale constructions like 3D-printed houses, showcasing the technology’s versatility (Interesting Engineering).
Comparative Analysis of Technologies
To illustrate the diversity, here is a table comparing key 3D printing technologies based on common attributes:
Technology | Common Materials | Primary Use Case | Precision Level | Cost Efficiency |
---|---|---|---|---|
FDM/FFF | Thermoplastics (PLA, ABS) | Prototyping, Education | Moderate | High |
SLA | Resins | Detailed Models, Jewelry | High | Moderate |
SLS | Nylon, Polymers | Complex Geometries, Functional Parts | High | Moderate to Low |
DMLS/SLM | Metals | Aerospace, Medical Implants | Very High | Low |
This table highlights the trade-offs between cost, precision, and application, aiding in technology selection (Protolabs, Aniwaa).
Conclusion
In summary, 3D printing continues to evolve, with key technologies like FDM, SLA, and SLS driving innovation across industries such as healthcare, aerospace, and education. The latest trends in material advancements, large-format printing, and sustainability highlight its growing impact, while groundbreaking projects like 3D-printed houses and advanced alloys showcase its vast potential. As the field progresses, staying informed through reliable resources ensures a deeper understanding of this transformative technology.